As we all know, not much activity is going on in the world at the moment; not just in the automotive sector but in any industry for that matter. However, that doesn’t stop the carmakers in helping the medical personnel in their battle against the COVID-19 pandemic. Skoda is among the few carmakers who are currently manufacturing/3D printing medical equipment.
The company is manufacturing respirators using state-of-the-art 3D printers. Check out some photos below showcasing the process.
The HP 3D printer that prints out the respirators.
The printer is capable of printing a set of 60 respirators in one go.
The printer prints the respirators in layers.
Respirator parts ready for delivery. In focus are the respirator exhalation covers.
Respirator parts in focus: seal plug and adapter.
Removing excess powder from the printed respirator mask.
Printing one batch takes 16 hours, followed by a cooling phase that takes roughly the same amount of time, Skoda said.
Everything was fine-tuned so that the respirators in a print batch were as close as possible without affecting each other so that the printing process was as efficient as possible. – Martin Sova, coordinator of plastics production and the 3D printing competence centre
One printed example in focus with excess powder removed.
The work bed from where the finished respirators are taken.
A printed CIIRC RP95-3D respirator.
Any company that owns one of the three types of Multi Jet Fusion 3D printer can now take part in producing the CIIRC RP95-3D respirators. They just need to contact the specialists at the Czech Technical University.
David Vaněk in production. He’s the head of the prototype and model construction department at Skoda.
The Czech Technical University opted for Multi Jet Fusion using the polyamide PA-12. This printing method ensures you get a homogeneous material that does not have distinct layers and is not porous. That is the key, because it means the traces of the virus do not remain in it and it’s easy to disinfect. – David Vaněk
The team working on respirator printing. L-R: Jaroslav Kafka, David Vaněk, Martin Sova.
The finished respirators can be disinfected and reused; its filters remain functional for up to a week, Skoda said. They are sent to the health ministry, which manages their distribution to the places that require the most.
These respirators are mainly intended for doctors and other front-line staff. It was developed by the Czech Institute of Informatics, Robotics and Cybernetics (CIIRC) of the Czech Technical University (CTU).
“We will keep supplying our 60 respirator sets a day for as long as they’re needed,” added Vaněk. Only when the situation allows will the 3D printer revert to its usual job of producing parts for Skoda.
Photos: Michal Čížek
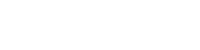
Leave a Reply
Note: Comments that are unrelated to the post above get automatically filtered into the trash bin.