Bugatti has produced a brake caliper via 3D printing, which the company claims to be the first in the world. Also claimed to be the largest brake caliper in the automotive industry.
Developed in association with Laser Zentrum Nord of Germany, the new brake caliper is made from Titanium instead of the current Aluminum alloy.
Mainly used in the aerospace industry the material offers considerably higher performance than aluminium. For example, even as a 3D printed component, it has a tensile strength of 1,250 N/mm2. This means that a force of slightly more than 125 kg can be applied to a square millimetre of this titanium alloy without the material rupturing. The new titanium brake caliper, which is 41 cm long, 21 cm wide and 13.6 cm high, weighs only 2.9 kg. In comparison with the aluminium component currently used, which weighs 4.9 kg, the weight of the caliper has come down by about 40% while ensuring even higher strength, Bugatti said.
To date, this approach was not feasible because it is extremely difficult or even impossible to mill or forge components from a titanium block due to the extremely high strength of the material.
The special 3D printer at LZN, claimed to be the largest printer in the world suitable for titanium, is equipped with four 400-watt lasers.
It takes a total of 45 hours to print a brake caliper. During this time, titanium powder is deposited layer by layer. With each layer, the four lasers melt the titanium powder into the shape defined for the brake caliper. The material cools immediately and the brake caliper take shape. The total number of layers required is 2,213. Following the completion of the final layer, the remaining titanium powder which had not melted is removed from the chamber, cleaned and preserved for reuse in a closed loop. What remains in the chamber is a brake caliper complete with supporting structure which maintains its shape until it has received stabilizing heat treatment and reached its final strength.
Heat treatment is carried out in a furnace where the brake caliper is exposed to an initial temperature of 700°C, falling to 100°C in the course of the process, in order to eliminate residual stress and to ensure dimensional stability. Finally, the supporting structures are removed and the component is separated from the tray. In the next production stage, the surface is smoothed in a combined mechanical, physical and chemical process which drastically improves its fatigue strength, i.e. the long-term durability of the component in later vehicle operation. Finally, the contours of functional surfaces, such as the piston contact surfaces or threads, are machined in a five-axis milling machine which takes another 11 hours to complete its work.
The result is a delicately shaped component with wall thicknesses between a minimum of only one millimetre and a maximum of four millimetres, Bugatti said.
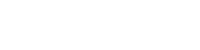
Leave a Reply
Note: Comments that are unrelated to the post above get automatically filtered into the trash bin.