Porsche has shared some more interesting, development-phase facts about the new 911 GT3 that debuted earlier this year. One of the highlights is that the car spent more than 160 hours in the wind tunnel fine-tuning its aerodynamics, especially the rear wing.
Speaking of which, its swan-neck mounting is similar to that of the 911 RSR which also influenced the 911 GT3 Cup car. Since two aluminium brackets hold the wing from above, the airflow can pass undisturbed across the underside, which is aerodynamically more sensitive. This new design led to a reduction in the flow losses and not only increased the downforce, but also resulted in a well-balanced negative lift, Porsche said.
We developed the aerodynamics of the new 911 GT3 in around 700 simulations. We spent more than 160 hours fine-tuning the car in the wind tunnel. – aerodynamics engineer Mathias Roll
The angle of attack of the rear wing can be set to four different positions and so is the front spoiler. “The new 911 GT3 generates 50% more downforce than its predecessor at 200 km/h (124 mph) just in the ex-works setting. In the setting with maximum downforce, the increase is as much as over 150%,” Roll added.
Not only are the components very similar to those used in our race cars, the development methods are also similar. In our ultra-modern wind tunnel in Weissach, we do not just drive straight ahead, we simulate every conceivable driving situation. We make the car roll, pitch and yaw in order to simulate the physical influences on the track. – Roll
The GT3’s high-revving, naturally aspirated, 4.0L flat-six motor was also subjected to torture tests. “In total, the engine in the new GT3 ran for more than 22,000 hours on the test rig. During testing, we repeatedly simulated typical circuit profiles and ran the engine at full throttle for a very high proportion of the time,” explains Thomas Mader, Project Manager for GT road car engines.
As in motorsport, precise valve actuation at high revs is delivered via rigid rocker arms. The proven VarioCam technology ensures camshaft control adapted precisely to engine speed and load condition. A crankshaft with large bearing diameters, wide connecting-rod bearings and plasma-coated cylinder liners ensure lower friction losses and reduce wear.
“The individual throttle valve system is taken straight from motorsport and significantly improves responsiveness,” adds engine specialist Mader.
When we have the same engineers who develop our race cars also working on the design of a new GT car for the road, that is the most direct technology transfer I can imagine. – Andreas Preuninger, Director, GT model line
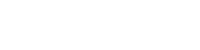
Leave a Reply
Note: Comments that are unrelated to the post above get automatically filtered into the trash bin.